Although steel hangar construction may seem to be fairly straightforward, there is much more to it than meets the eye. From evaluating appropriate dimensions to wiring the building correctly to offering secure but easy access for your aircraft, the decisions that need to be made add up to a significant project. Aviation projects require extreme precision and can be a difficult undertaking.
An airport hangar must be functional while offering security and protection for the aircraft and machinery it houses. The use of steel provides numerous benefits, including strength, durability and weather resistance. When designing and building a steel airplane hangar, start by considering the functionality and sustainability of the building. This article addresses key factors to keep in mind as you begin your aviation project.
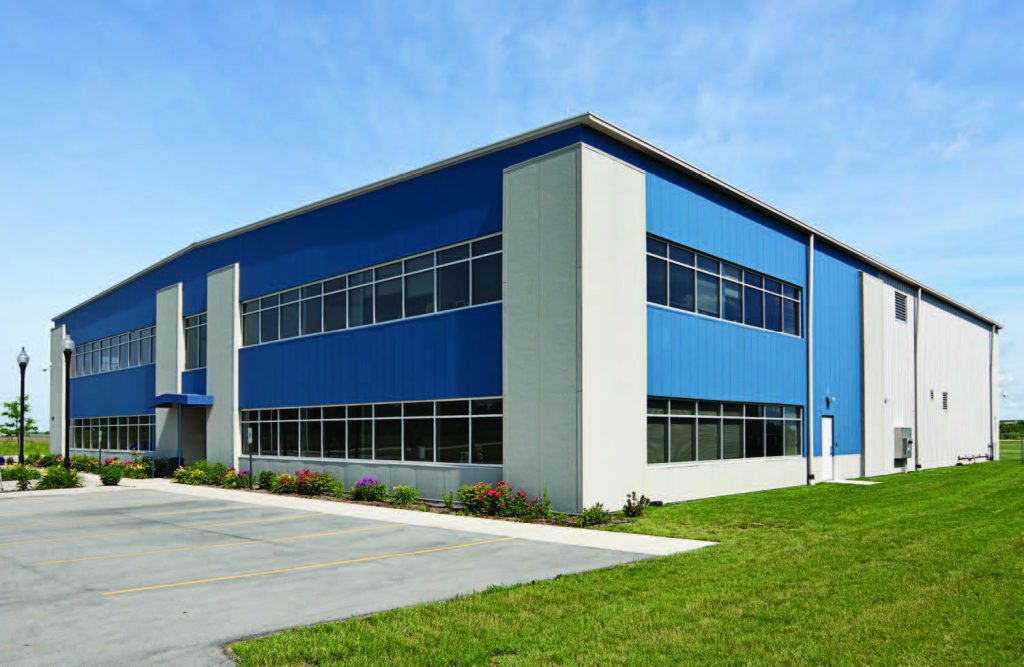
Determine your budget
Establishing a budget is one of the first steps to take in the construction of an aviation facility. The cost of building a steel hangar can vary depending on a multitude of factors, including the type of roof installed (screw down or standing seam) and the type of aircraft doors (vertical lift, sliding, bi-folding). Often overlooked by owners are the expenses of site work and meeting numerous code requirements. Early code reviews will aid in site planning and estimating.
Knowing your budget limitations and investigating factors that drive costs will help you understand the type of hangar that will best fit your needs and your budget.
Choose the site
Work with your engineering consultant to choose the best location for the new hangar while considering future plans. Larger hangars, specific hangar uses, or a hangar in close proximity to other buildings/hangars may require code-driven fire suppression systems or rated firewalls, both of which can be costly. Are there special requirements for stormwater runoff on the property? How far are utilities from the planned hangar? Are the soils stable enough to support the structure? Will soils need to be imported or exported? Can exported soils be dumped somewhere else on the airport property to save transport costs? Will there be demolition of an existing building, and would it require abatement (lead paint or asbestos) before demolition? All these aspects can greatly impact the project’s budget and need to be considered early on as the location is being selected.
Choose the proper hangar size
When determining the size and dimensions of your airplane hangar, keep in mind how you can best use the available square footage. Using space efficiently is critical in aviation construction.
Consider not only the airplanes that will be housed, but also the room needed for moving the aircraft and positioning equipment such as ramps and stairs. Plan for workflow and workspace for the maintenance crew when repairs are required. Your architect, during the design phase, will help create a plan for support columns that are adequately load-bearing but also placed appropriately to ensure maximum open space.
The size and specific use (storage, light maintenance, heavy maintenance, material storage, etc.) of the hanger is another critical factor that will drive fire suppression or rated wall requirements. Again, early code reviews by the architect and civil engineer will help flush out any fire-related code requirements.

Prepare for heavy loads and high traffic
Airport hangars will encounter ultra-heavy loads, high abrasion and harsh chemicals. It is vital to design and build footings and select flooring that will hold up to the stress.
Due to the massive pressure planes put on the foundation and floors, aviation hangars require concrete foundations. A concrete slab foundation made from reinforced concrete, which is typically inexpensive and can be built quickly, is commonly used for hangars. Or, your building may require a pier foundation, consisting of concrete piers or beams set deep into the ground that will bear the weight of the hangar and aircraft.
Furthermore, the type of flooring used is important. Hangar facilities require a hard aggregate concrete that can hold up to the pressure and stress of heavy weight. The finish coating needs to be thick, durable and chemical-resistance. Avoid a shiny finish or poly coat, and instead, go with an epoxy coating with “grip” to provide traction for easily moving planes in and out. Your aviation construction company will recommend materials that protect your hangar against aggressive wear and extend its life expectancy.
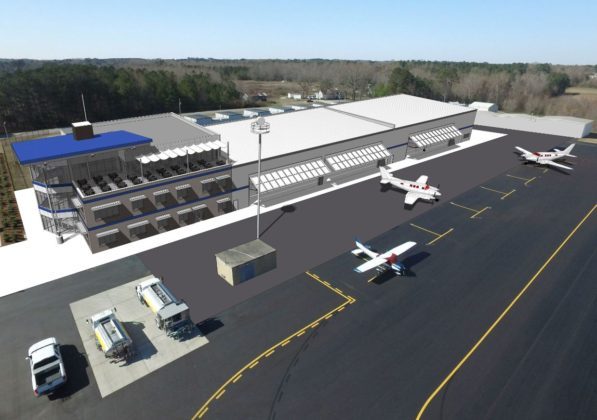
Determine hangar access
In the design phase of your project, your architect will help you define access into and out of the hangar. For a single-plane hangar, the entry and exit points may be obvious. For multi-aircraft hangars, however, the efficient movement of aircraft in and out of the facility can be more challenging.
To ensure the design of the hangar is as open as possible, carefully determine the required size of the doors. You will position the hangar based on its entry and exit points rather than merely adding a door to the hangar. Door design should maximize accessibility. When choosing the main hangar door, there are three options to choose from:
- Bi-folding doors – doors that are horizontally split down the middle and fold in half when activated; some can create a canopy when fully open
- Vertical lift doors – dual track standard doors, like a garage door
- Sliding doors – steel airplane hangar doors that follow a track and slide side to side
Sliding doors are often the most affordable option, while bi-folding and vertical lift doors offer the best space savings.
A fly-through hangar has a second door at the back of the building for planes to go in and out at either end. Fly-through hangars are ideal if you have multiple planes and want to park them one behind the other.
You will also need personnel doors in your hangar. Include standard or double doors for people to safely go in and out.
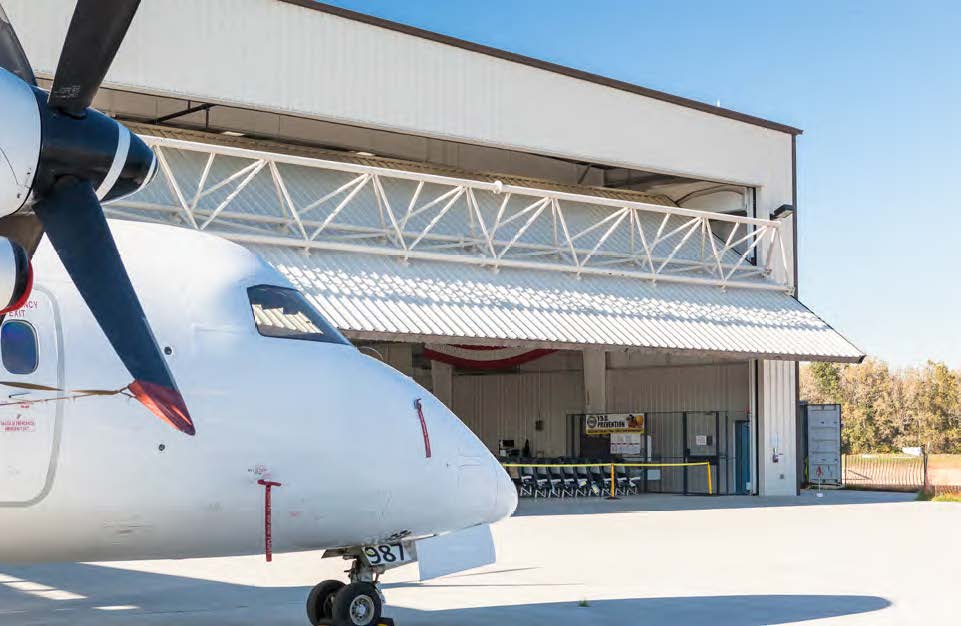
Plan ahead for electrical requirements
When designing an aircraft hangar, map out your electrical needs and plan your wiring strategy during the design phase. Easy access to multiple power outlets will be essential for servicing and maintaining the aircraft, but wires can often be in the way of traffic flow if not properly placed. Outlet banks may be needed throughout the building; these can be connected to columns or permanent scaffolding.
Think about lighting
Lighting is an easy aspect to overlook when designing an aviation facility. But the vast open space of an airplane hangar requires a large amount of light, which takes planning. A good rule of thumb when designing a hangar is to create a lighting plan, then double it. Install skylights where you can to make use of natural light. Also, think about how these lights will be accessed when bulbs need to be replaced.
Find an experienced aviation construction company
Not every architect and construction company have the knowledge to design and build an aviation facility. Aviation construction is a complex job, and you need a team who is experienced in hangar design and metal building construction. A skilled design-build team will be able to walk you through all FAA requirements, code reviews and permitting, making the process easier for you.
Bobbitt has years of experience designing and building metal buildings for all types of heavy-duty industrial application, including aviation projects. With our comprehensive design-build process, we handle all aspects of the job under one contract and one single point of responsibility. Contact us today to discuss your aviation project.