The popularity of pre-engineered metal buildings (PEMB) in commercial construction has continued to grow over the past decade. Because of the energy and cost efficiencies of PEMBs, building owners can expand faster and more cost-effectively than ever before.
From industrial facilities and warehouses to restaurants and medical offices, pre-engineered metal buildings have proven to be a preferred solution for a variety of projects. Having spent more than 20 years in the metal building industry, Bobbitt Project Developer Andy Speck, PE, knows the ins and outs of this construction method. In the following interview, he explains the multiple advantages of PEMBs compared to traditional construction.
Q: What is a pre-engineered metal building?
SPECK: A PEMB is a cohesive metal building system consisting of rigid frames, cold-formed steel secondary structural members, building bracing members and typically metal panels on both the roof and exterior walls. All building components are manufactured offsite in a controlled environment and then shipped to the building site to be erected.
As a Butler Manufacturing builder, Bobbitt uses a detailed structural design process to order the pre-engineered building materials from Butler. After fabrication, Butler provides the final erection drawings and a bill of materials, including all parts and pieces that will ship – from the columns and beams down to the nuts and the bolts used to complete the building.
PEMBs are an excellent option for any building that requires clearspan, or column-free, interiors and ample clearance. By avoiding the use of columns, PEMBs provide more usable interior space. Once only used for warehouse and storage facilities, pre-engineered metal buildings are cropping up in office buildings, schools and even churches.
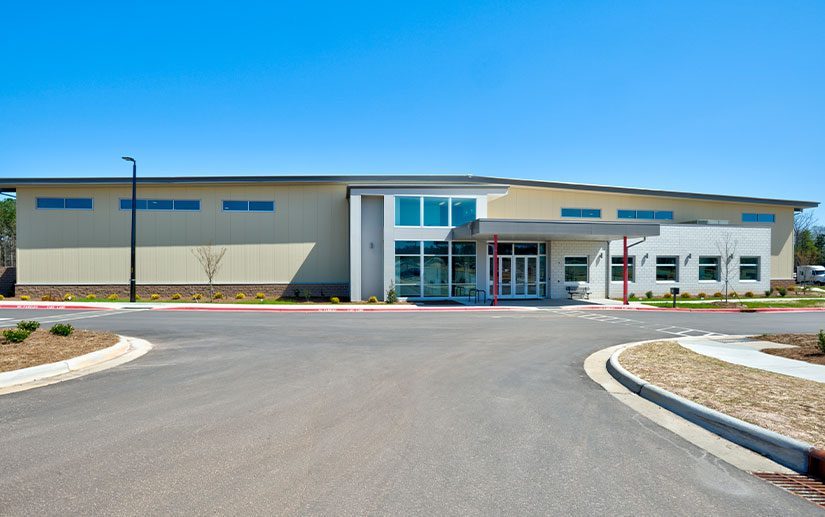
Q: Do PEMBs help with speed of construction?
SPECK: Absolutely. PEMBs result in shorter construction times compared to traditional conventional steel systems where builders must do a lot of field work to complete the structure. The PEMB components are designed to fit together precisely, with little to no field cutting or welding, thus saving time in the field.
Another benefit is less interruption to business operations. Whether we are building a new facility, renovating or expanding, pre-engineered buildings allow owners to get back to business faster.
Q: What are the PEMB costs compared to traditional construction?
SPECK: Because of the numerous efficiencies gained, pre-engineered metal buildings cost less than traditional construction from the ground up. With the detailed fabrication work performed offsite in a factory-controlled environment, there is less material waste on the job site. With strategically designed and detailed structural members, steel is used only where it is needed. This efficiency means you won’t be paying for material that isn’t used. The speed of construction, allowing for quicker building occupancy, also means a reduction in lost profits due to prolonged construction times.
Q: What are some of the advantages of steel building construction?
SPECK: Steel, in general, has an excellent strength-to-weight ratio. Steel erection is not impacted by cold like concrete is, and steel is much more fire tolerant than many materials used in buildings. It comes with no risk of mold or rot, and as long as it is properly protected, steel won’t rust.
Bobbitt, for example, uses Butler’s G30 galvanized acrylic-coated steel for minimal maintenance for owners down the road. Steel is also able to withstand harsh natural elements such as strong winds, heavy snow loads and severe seismic events.
Furthermore, the Butler MR-24 standing seam roofing system is second to none. Durable and robust, if kept clean and free of debris, this roof has the potential to last 50 years or more. MR-24 outperforms traditional roofs that would need to be replaced three to four times during the same 50-year span.
Q: How does the PEMB construction method stack up in terms of sustainability?
SPECK: Steel is the most recycled material in North America. Melting scrap steel consumes 80% less electricity than making steel from scratch. You can also recycle steel without affecting the quality of the renewed material. PEMBs are typically made from 100% recycled steel, yielding a low carbon footprint.
Offsite fabrication also reduces construction equipment emissions. Because you can control the exact size of the components, you have less scrap and unused material once the building is complete, creating over 50% less jobsite waste than other construction systems.
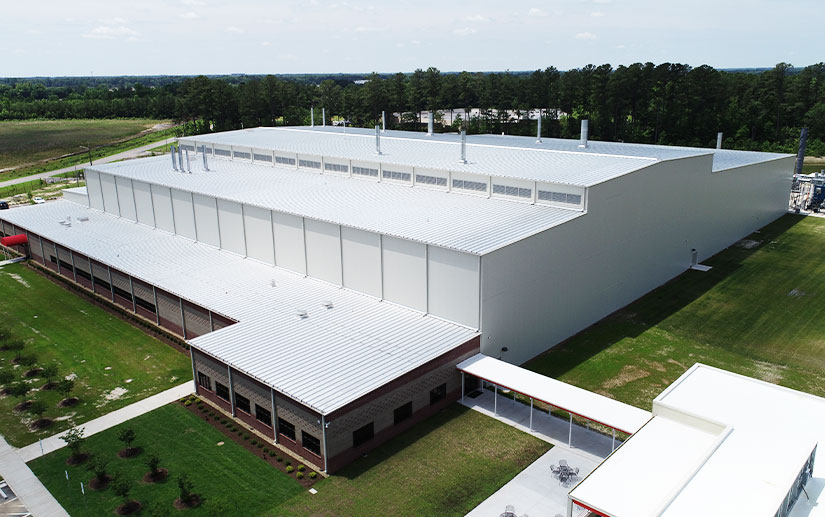
Q: Does the building owner have to compromise on design and aesthetics with metal building construction?
SPECK: Definitely not. That’s a common misperception. When it comes to the aesthetic appeal of PEMBs, you are limited only by your imagination. Bobbitt has created countless buildings you would never guess to be pre-engineered. Exteriors can be finished with stucco, brick, glass, precast concrete and other materials to achieve the desired look.
This is all addressed during the design phase of the project, and the design-build method really stands out when using a PEMB system. Our architects can easily customize PEMBs to give you the look you want, delivering the best of both worlds.
Q: What about future building expansion?
SPECK: Should you need it, PEMBs allow for easy expansion down the road. The capacity for future expansion can be included in the original building design or addressed later with separate framing. In both scenarios, the old and new buildings appear seamless.
PEMBs can also be easily replicated. Should you need a uniform appearance across multiple locations, PEMBs are a perfect choice and can be customized as needed.
Q: What are Bobbitt’s qualifications for erecting pre-engineered metal buildings in the Carolinas?
SPECK: Bobbitt has worked in the metal building industry for more than 70 years and is a major partner of Butler Manufacturing, the leading supplier of steel framed building solutions for community, commercial and industrial uses. Bobbitt’s in-house design capability and construction expertise are unmatched for this type of work in North and South Carolina.
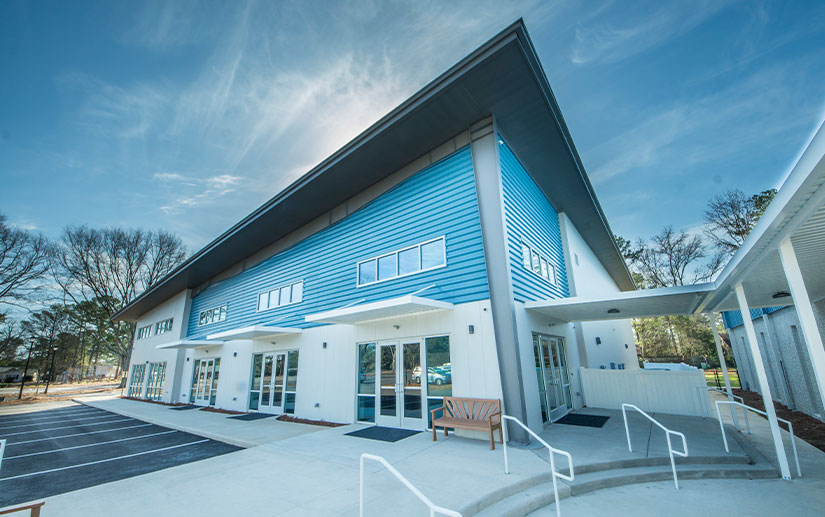