Industrial companies with manufacturing, distribution and warehousing operations face a common challenge of shrinking budgets and the need to do more with less. This is especially true as it pertains to maintaining your facilities to optimize production, manage inventory, ensure efficient distribution and maintain ISO certification. For the industrial sector, it’s more important than ever to design and construct facilities that support growth and ensure compliance.
Your company can best meet these goals by embracing the “new” standard in architectural design and construction: DESIGN-BUILD. This method for building brings together all aspects of project planning, site design, architectural design, permitting and construction – all delivered by a single source.
View Bobbitt Projects:
Rebirth of Design-Build as the Preferred Approach
In reality, design-build isn’t new at all. From a historical perspective, and contrary to popular belief, utilizing separate design and construction teams is actually the non-traditional approach. For centuries, master builders served as the chief architect, engineer and builder all in one. The efficiency and precision of this model is exemplified in renowned structures such as the Great Pyramids of Egypt and the Parthenon in Greece. In more recent times, American structures such as the Brooklyn Bridge and the Pentagon were built using integrated design-build.
These master builders accepted full responsibility for their projects, combining conceptual design with the logistical challenges of the construction process. Yet, the process fell out of favor through the Industrial Revolution. Significant cost efficiencies and the ability to reduce construction timelines have led to a strong resurgence of design-build for large facility projects.
In fact, the United States government, the largest purchaser of construction in the world, has a stated goal to utilize design-build in 75% to 80% of its new construction projects. In MILCON conferences throughout the Southeast, the reasons given to support this goal are that design-build saves time, saves money, and in the end, entails less litigation.
Design-Build Compared to Other Construction Methods
The design-build process has numerous advantages over general contracting (also known as design-bid-build) and construction manager at-risk methods, in which multiple vendors are loosely connected in delivering various aspects of the project. Building owners often get hit with unforeseen costs and delays when architectural design is performed in a vacuum, without close collaboration with the construction team. In contrast, the design-build method of construction saves time and money for the building owner (see chart).
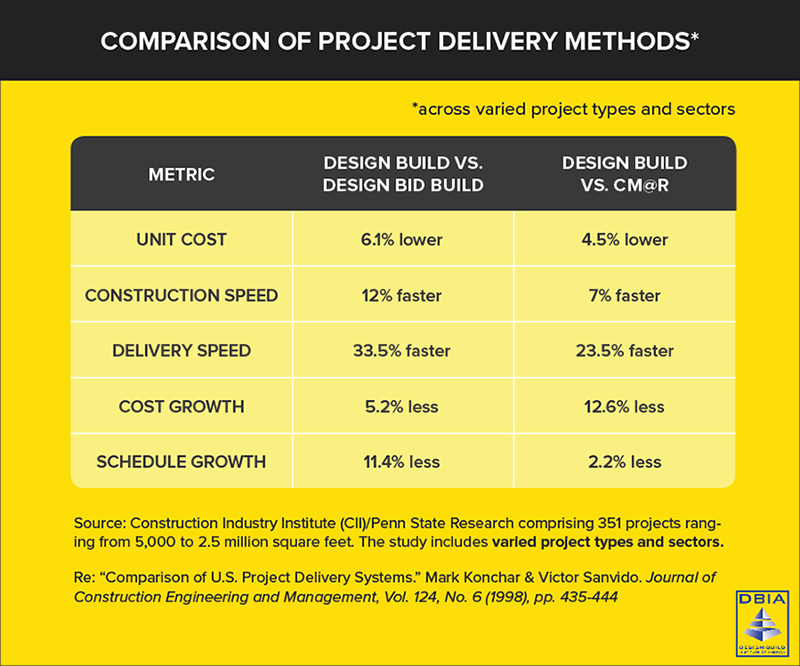
Advantages of Design-Build for the Industrial Sector
Time savings, monetary savings and reduced litigation are achieved through the close collaboration of your design-build team. This approach consistently outperforms other construction methods. Here’s how:
- Single source of responsibility – With a design-build contractor, you get the entire team – taking your project from initial planning, conceptual drawings, final architectural plans and permitting to construction and final facility completion. This eliminates finger-pointing between the architect and general contractor. Furthermore, this team approach has big benefits when it comes to your architect designing to your budget and your contractor being able to build what the plans specify.
- Expert project management – Your design-build company serves as a consultant to your senior management team and to your facility planners and managers, enabling you to make informed decisions to benefit your industrial building project. The design-build firm is the facilitator who pulls all the different design elements, regulatory requirements and budgetary requirements into a cohesive plan.
- Cost savings – With the old design-bid-build method, you don’t find out the cost of your building until you send the drawings out for bid, and by then, it’s often too late. Change orders to bridge the gap between the design and the construction realities can become very costly during the construction phase. With design-build, budgeting is done during the design phase, enabling the architects and construction team to verify costs. This collaboration yields in an average cost savings of 6%.
- Streamlined delivery – The design-build process offers rapid delivery, because design and construction happen concurrently and the time-consuming bidding phase is eliminated. This results in significantly faster project delivery – up to 33% faster, according to industry studies.
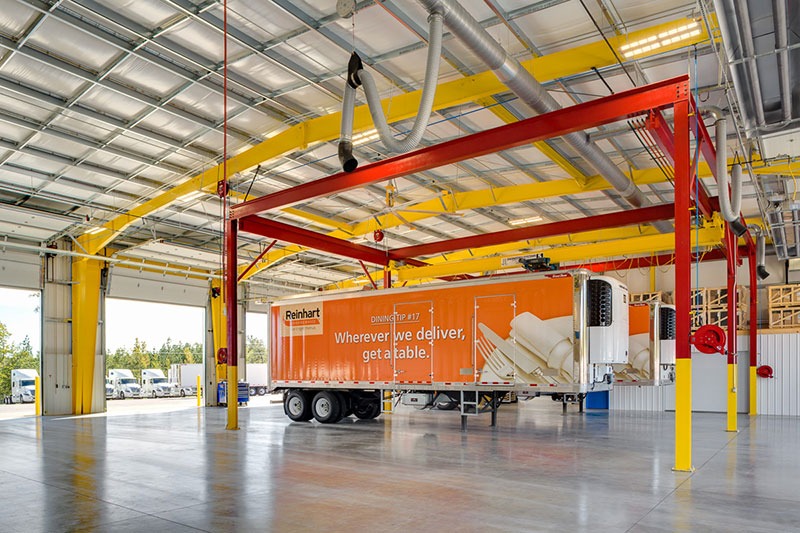
Thermo King – Gaston, SC. View the Industrial & Distribution portfolio.
Selecting the Best Design-Build Firm for Your Industrial Facility Project
If the benefits of design-build sound like a fit for your warehouse, plant or distribution center, then the next step is to vet potential design-build companies. Ask these critical questions to source a top design-builder for your industrial project.
- Is your company a true design-build firm, with in-house architects that work with your construction personnel day in and day out?
- What is your track record with projects in the industrial sector?
- Can you show me your portfolio of projects that are similar to mine?
- Tell me about your company overall – its history, financial stability, greatest strengths, etc.
- Walk me through your process and tell me what to expect if my company decides to hire your firm.
- What would my design-build team look like?
- Can you provide references from several clients in my industry?
Design-Build – The Bottom Line
Design-build is quickly becoming the new standard in industrial construction. Whether you are building a new facility, renovating or adding on, this approach can offer tremendous advantages for your company. The process allows for the natural integration of design and construction, thereby providing insights into the costs and constructability of various designs. The end result is a sound design, a defined budget and a streamlined schedule.